Quanser Autonomous Vehicles Research Studio
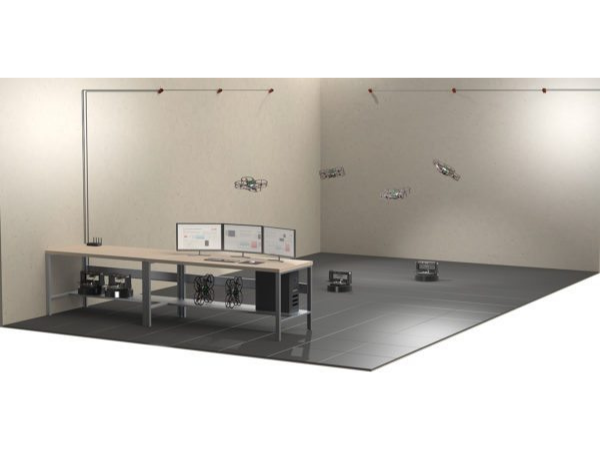
Quanser Autonomous Vehicles Research Studio
A comprehensive teaching and research station with autonomous and collaborative robots. It consists of flying and mobile robots, a control and monitoring station, a motion capture system and safety equipment (nets, floor mats, etc.)
INQUIRY
Your data is the data that allows us to make the first business contact. All data provided in the form are treated as confidential. Personal data appearing in the form will be processed in accordance with our privacy policy, available at www.edu4industry.com.
Base station:
- PC with Windows 10 Professional operating system, 6-core Intel processor, 32 GB RAM, hard drives: 256GB SSD, 1TB HDD
- High performance GPU
- USB keyboard, USB optical mouse
- 3 monitors 24”
- QUARC- add-on to Matlab / Simulink. Note - Matlab / Simulink licenses not included in the package
- USB controller
- Wi-Fi router with built-in processor and 802.11ac standard support with a speed of 1,900Mbps
Flying Robot:
- 4-rotor configuration (quadrotor), permissible load 300g, power supply: Li-Po 11V batteries with a capacity allowing for min. 10minutes of flight under max. load,
- Built-in programmable control platform Intel Aero Compute board, 64-bit 4-core processor, 4GB of RAM DDR3-1600, 8x PWM, 2x UART, 3x SPI, 4x ADC, 3x encoder input, 5x GPIO
- Main camera for orientation in the area: stereoscopic 3D Intel RealSense R200 (RGB camera, 2 IR vision sensors), depth of field of view 3m, resolution 1080p HD @ 30fps, VGA @ 60fps), additional camera for ground observation: VGA resolution @ 120fps
Ground Robot:
- Programmable control platform with 2 driven wheels - Kobuki Mobile Base platform, diameter: 35 cm, height: 27 cm, permissible load 4.5 kg, power supply: Li-Po batteries with a capacity allowing for 2 hours of work under max. load, max. linear speed 0.7 m/s
- Built-in control platform: programmable with open architecture: Raspberry Pi 3B + (4-core Cortex-A53 1.4GHz processor) with integrated Wi-Fi communication module b / g / n / ac
- Microsoft Kinect RGBD motion sensor
- Other sensors: tactile crash (3x), distance (range from 0.5 to 4m), wheel drop (on 2 wheels), ground fault (on the housing), 3-axis gyroscope, wheel rotation angle encoders, color programmable LEDs (2x), IR proximity sensors for orientation in the environment
- Expansion inputs/outputs: 24 configurable I/O channels, ADC converters (2x), PWM (4x), encoder inputs (2x), UART, SPI, I2C, USB ports (2x), 1GB Ethernet, MIPI CSI camera port, port MIPI DSI for connecting a touch panel
- Environment orientation camera: VGA @ 30fps resolution
Additional equipment:
- Motion capture system in the working space: Natural Point OptiTrack Flex 13, number of cameras depends of the size of the laboratory
- vertical networks securing the working space with mounting brackets
- Foam floor mat protecting the working area
- Battery chargers for drones and wheeled robots (1 charger per vehicle)
Sample research topics:
- Control of a single flying and driving robot (manual and automatic mode),
- Vision of the location
- Communication between robots
- Cooperation between robots
- Mapping
- Navigation
- Multi-agent systems(swarm)
- And others